Pharma and Fine Chemical Industry Needs for Green Innovation
In an article published just over 10 years ago now, a roundtable from top companies in the pharmaceutical and fine chemical industries highlighted some of the many needs for making chemical manufacturing greener and more sustainable. They highlighted some key areas including continuous processing, separation/reaction technologies, solvent recycle and solvent optimization as areas that needed research if the industry were to turn a greener leaf.
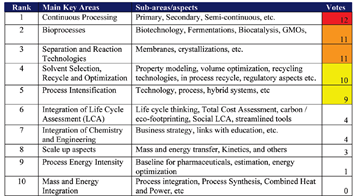
Survey results from roundtable members
10 years later many of these goals are becoming achievable through innovation by equipment suppliers, most notably in flow reactors, flow separators, and bioreactor technology. Following the availability of the technology, some companies have readily taken up the ideas of continuous processing and flow, yet others still lag behind, often citing a lack of in-house expertise in these areas. Hopefully, this education gap will be closed in the coming years as companies pay more attention to these areas and universities deliver students ready to contribute. Further, as flow technologies scale ever larger, there is the possibility to bring more and more processes in to a continuous or semicontinuous (hybrid) manufacturing approach.
Of particular interest is the focus that the roundtable paid to separation and workup technologies, which is often forgotten behind the “focal point” of the process – the reaction. They point out that “For every 2 reactions, approximately 2 extractions, 1 distillation, 1 crystallization, 1 product isolation, 1 product drying step, and 0.5 nonproduct filtration steps are performed.
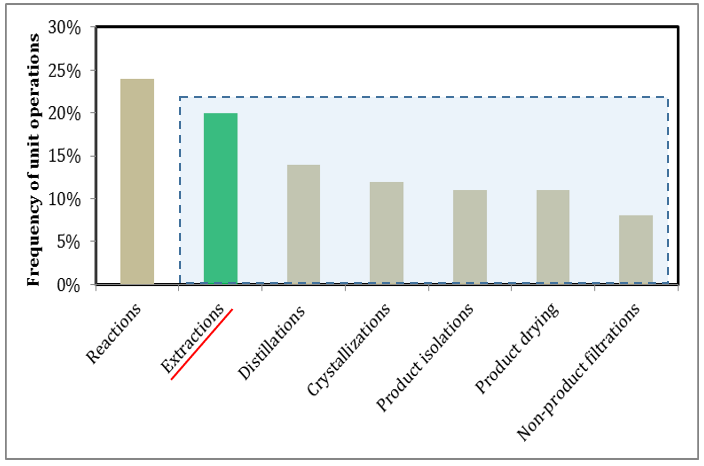
Frequency of Unit Operations
Naturally, this leads to the question: How can I make my workup greener?
This question is well answered in the paper (which is very much worth the read!), coming from Zaiput, though, the focus always comes to flow. Of course, bringing steps of your work up into flow can leverage the advantages that flow provides more broadly, including increased heat transfer (lower consumption), better process control (less loss), and quick scaleup (less waste). One technology of particular interest is counter-current extraction, which can dramatically reduce the amount of solvent needed to carry out extractions. Certain technologies like membrane extraction platforms can do so at a very low energy input – providing a further advantage over traditional methods like centrifugation.
As these technologies further mature, I’m hopeful that companies in the Pharmaceutical and Fine/Specialty chemical industries will adopt greener chemical manufacturing methods – the planet needs it now more than ever.
For the full paper published in OPR&D, please see: https://pubs.acs.org/doi/10.1021/op100327d